H & B DIVERSION PLOUGH FOR BHP JIMBLEBAR STAGE 2
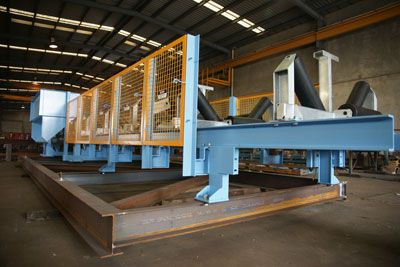
H & B Mining have just completed fabrication of a conveyor module which includes a carry belt diversion plough as an integral part of the design for Jimblebar Stage 2. The fully transportable conveyor module required for conveyor CV002 was designed by H & B’s in-house design team and fabricated in the Welshpool workshop. The fully assembled CV002 conveyor module completed factory acceptance testing last week and is now ready for dispatch. The fully transportable conveyor module has been designed to carry a 1600mm wide belt travelling at a maximum speed of 6.09 m/sec and handling a maximum of 11000 tonnes per hour.
The inclusion of the carry belt diversion plough on this section of conveyor allows the conveyor to function normally whilst the diversion plough components lie dormant beneath the operational conveyor belt. For the diversion plough to become operational, the tilt idlers that lie dormant under the belt need to be activated to lift up under the carry belt and flatten the belt to interact with the fixed scraper. Any material on the belt is diverted off the belt and into the chute mounted on the side of the conveyor.
As part of the scope of work, H & B designed the conveyor section with a diversion plough inclusion to be transported in one piece. This involved designing and supplying a transport frame and lifting beams to allow for the fully assembled conveyor section to be lifted onto a truck and transported to site in one piece.
The previous success of H & B Mining diversion ploughs installed on conveyors CV001 and CV112 in Stage 1 Jimblebar, encouraged BHP Billiton to stick with the same recipe. The conveyor section is expected to be delivered to site on May 20th 2016 with installation expected to follow immediately.
Go to www.handbmining.com.au or phone (08) 9403 2993.
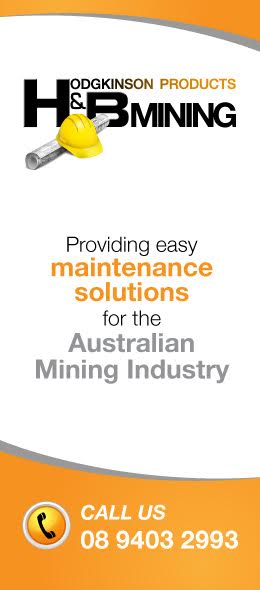
Latest News
WORKSHOP
7 41 Division Street,Welshpool,
Perth, Western Australia 6106
- Tel: 08 9403 2993
- info@handbmining.com.au
HEAD OFFICE
7 Tahiti Lane, Hillarys, Perth, Western Australia 6025
- Tel: 08 9403 2993
- info@handbmining.com.au